
安徽伟工机械科技有限公司
经营模式:生产加工
地址:芜湖县机械工业园榆林路1388号
主营:电涡流缓速器组件,车辆配件,阀门及配件,工业管道配件研发
业务热线:1386-8888645
QQ:1353026929
一、水玻璃型壳
安徽伟工机械精密铸造水玻璃型壳这一工艺在国内已有近50年的生产历史,经过精铸界同仁个半世纪的不懈努力,水玻璃型壳工艺的应用和研究已达到了很高水平。多年来由于背层型壳耐火材料的改进和新型硬化剂的推广应用,水玻璃型壳强度有了成倍增长。低廉的成本、短的生产周期、优良的脱壳性能及高透气性至今仍是其他任何型壳工艺所不及的优点。
二、复合型壳
与水玻璃型壳相比,其铸件表面质量有了很大提高,表面粗糙度降低、表面缺陷减少、返修率下降。可应用于不锈钢、耐热钢等高合金钢。生产周期则比低温蜡-硅溶胶型壳短得多,与水玻璃型壳相近。
三、硅溶胶(低温蜡)型壳
这一工艺符合国情,在铸造1kg以上,特别是5kg以上中大件铸件时,具有更大的适应性和优越性。比复合型壳质量稳定,尤其是铸件尺寸精度高,因它没有水玻璃存在,型壳高温性能好,在1000-1200℃焙烧后型壳透气性高,抗蠕变能力强,既可适用于薄壁件,复杂结构的中小件,又可生产重达50-100kg的特大件,如水泵、叶轮、导流壳、泵体、球阀体、阀板等。对于薄壁中小件或大件可以采用叉壳或抬壳在炉前直接浇注,更可获得高成品率。
四、硅溶胶(中温蜡)型壳
这是国际上通用的精铸件生产工艺,它具有高的铸件质量、低的返修率,特别适合于表面粗糙度要求高,尺寸精度高的中小件、特小件(2-1000g)。但由于设备及成本限制,较少应用于中大件(5-100kg)。





熔模铸造的制模工艺
按照模料的规定成分和配比,将各种原料熔融成液态,混合并搅拌均匀,滤去杂质浇制成糊状模料,即可以压制熔模。压制熔模普遍采用压制成型的办法。该方法允许使用液态、半液态以及固态、半固态模料。液态和半液态模料在低的压力下压制成型,称为压注成型;半固态或固态模料在高的压力下压制成型,称为挤压成型。无论是压注成型还是挤压成型,都必须考虑充填和凝固时的优缺点。
(1)压注成型
压注成型的注蜡温度多在熔点以下,此时模料是液、固两相共存的浆状或糊状。呈浆状的模料中,液相量显著超过固相量,所以仍保留着液体的流动性。在这种状态下压注,熔模表面具有较低的粗糙度,而且不易出现由于紊流、飞溅带来的表面缺陷。糊状模料的温度比浆状模料更低,已失去流动性,虽少有表面缺陷,但却具有较高的表面粗糙度。
模料压注成型时,在保证良好充填情况下应尽量采用低的模料温度和压型工作温度。压力的选择并不是越大越好,虽然压力大熔模收缩率小,但压力和压注速度过大,会使熔模表面不光滑,产生“鼓泡”(熔模表皮下气泡膨胀),同时,使模料飞溅出现冷隔缺陷。在制模过程中,为了避免模料粘附压型,提高熔模表面光洁度,应使用分型剂,特别是对于松香基模料。
(2)挤压成型
挤压成型把在低温塑性状态下的模料挤压入型腔,在高压下成型,以减少和防止熔模收缩。挤压成型时的模料处于半固态或固态,该模料在正常条件下比较硬,但在高压下能够流动,其特点是粘度大。因此挤压时压力的大小取决于模料的粘度及在注料孔和型腔中的流动阻力。模料的粘度愈大,注料孔径愈小,型腔尺寸愈大而横截面积愈小以及模料行程愈长,则模料流动时的阻力愈大,因此需要愈高的挤压压力。采用半固态模料挤压成型,熔模的凝固时间缩短,因而生产率,特别适用于生产具有厚大截面的铸件。
不锈钢精密铸造技术根据温度怎么进行划分?
有些厂家是使用不锈钢精密铸造来加工产品的,都是只需要少量加工或者不再加工就可以符合产品尺寸要求的成型技术,按照不同的方式也会分为不同的工艺。
不锈钢精密铸造管件厂家今日来为你介绍按照成形温度的划分:
1、热锻工艺,能够在结晶温度以上来进行不锈钢精密铸造,当变形温度高时,不锈钢精密铸造材料的变形抗力会低,但是塑性会好,大多数都是用来加工形状复杂的产品,例如托轮。
2、冷锻工艺,在室温状态下进行不锈钢精密铸造的工艺,室温成型能够有效避免热胀冷缩带来的尺寸误差,精度相对来说比较好控制,锻件的表面不会出现氧化或烧损等等。
3、温锻工艺,能够将金属加热到结晶温度之下就能进行不锈钢精密铸造的技术,可降低设备与模具的载荷量,提高金属的塑性以及流动性,不用退火。
4、复合锻工艺,是将冷、温、热锻工艺组合完成的一种不锈钢精密铸造工艺,同时能够发挥冷、温、热锻的优点,也能够避免其的缺点。
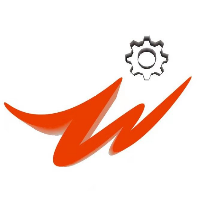
张经理先生
手机:18949552994